
“There are constant design changes and constant upgrades. “Part numbers that used to last a decade now last for a year at best,” he said. The general trend in manufacturing is toward finishing parts with one setup and minimal handling, affectionately referred to as “one-and-done.” The drive towards mass customization is a key reason, observed David Fischer, lathe product specialist at Okuma America Corp., Charlotte, N.C.
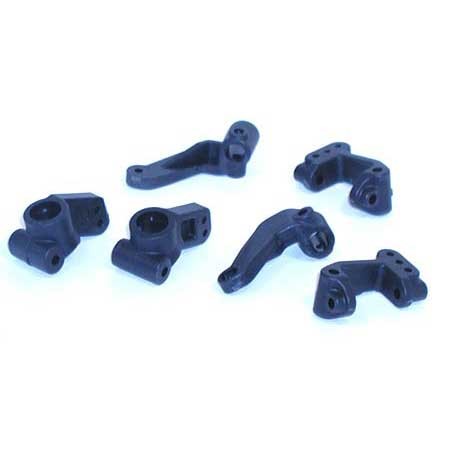
A turret station can be used as a tailstock, as shown here.
#Team z front spindles full
Okuma’s MULTUS has a true milling spindle on an articulating B-axis for full five-axis machining. That makes fast work out of complex parts. “You can have five independently engaged tools while the part is being held in the main spindle and then cut it off and move it to the sub-spindle and then engage one tool at a time,” explained Judt. (The sub-spindle grabs the part before cut-off and holds it for subsequent machining.) And if the parts require cross-drilling or other non-turning complexities, the argument for the newer multi-function lathes becomes compelling.Īs Judt put it: “My twin-spindle machines costs a lot less than two or three or four single-spindle machines and a vertical machining center.” It is not an unfair comparison because the LICO twin-spindle to which he refers doesn’t just have a sub-spindle that holds the part to machine the “other end.” It also features three or four independently programmable cross-slides mounted around the main spindle and a turret with live tools for side drilling and milling. Maybe it goes on another machine that does Op 30 and so on.” But, he added, the price difference between a single-spindle and a multi-spindle lathe “isn’t that big anymore, especially when factoring in labor.”Īfter all, the simple addition of a sub-spindle provides the ability to machine all six sides of the part without handling it. “They do Op 10 of a part and then put the part into another machine, which does Op 20. Judt said he usually finds single-spindle lathes in smaller shops. This points to the second reason for buying a single-spindle machine: budget. So these machines end up being labor intensive if users are forced to re-clamp parts that require machining on both ends. But according to Phillip Judt, applications engineer at Absolute Machine Tools Inc., Lorain, Ohio, the problem is that there aren’t many such parts. The first is easy: parts that can be completed from one end. When it comes to lathes, there are probably only three situations in which a single-spindle configuration is the right choice.
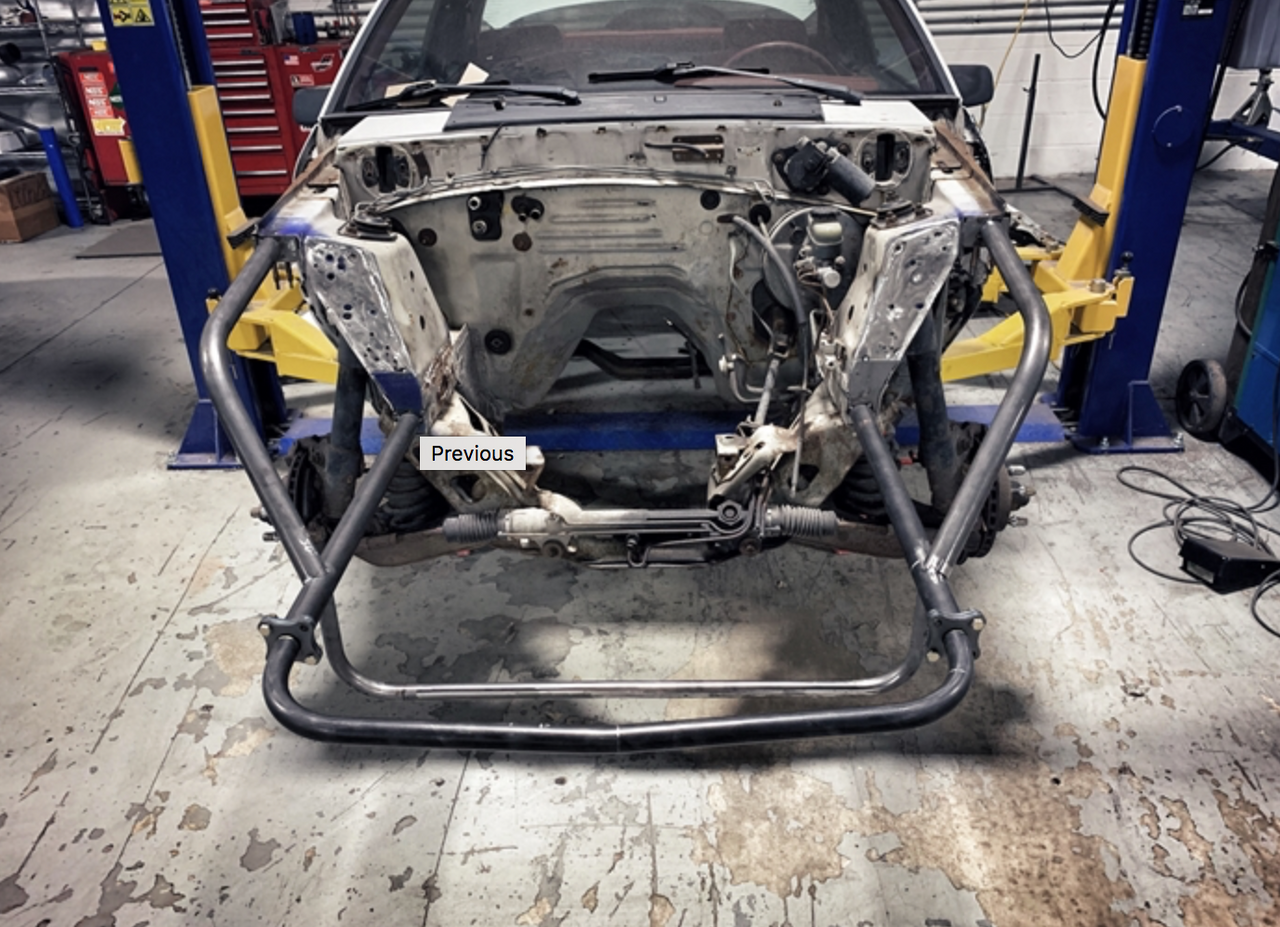
What are the tradeoffs that have driven these choices and are they changing? In mills, the spindle holds the cutting tool and most machines have just one. In lathes, the primary spindle holds the part and it’s common to have more than one. The spindles rotate in a drum so each station attacks the part in turn, producing complex forms in seconds.
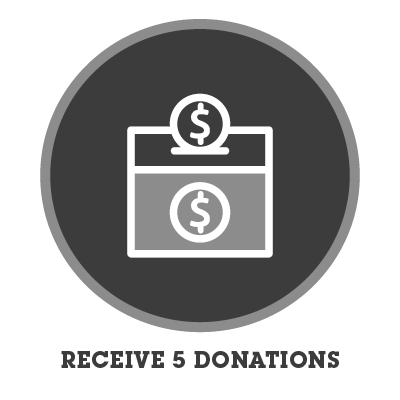
An Index MS lathe simultaneously machines on six independent part spindles (three visible here). But one of the basic ways to differentiate between machine tools is by counting spindles. There are seemingly endless variations in how milling and turning machines are equipped, including mill-turn and turn-mill combos.
